Title |
Programming Anisotropic Functionality of 3D Microdenticles by Staggered-Overlapped and Multilayered Microarchitectures |
Author list |
Park, Jeong Eun; Je, Hyeongmin; Kim, Chae Ryean; Park, Sudong; Yu, Yeonuk; Cho, Woongbi; Won, Sukyoung; Kang, Dong Jun; Han, Tae Hee; Kwak, Rhokyun; Lee, Seung Goo; Kim, Sanha; Wie, Jeong Jae |
Publication date |
2024/02/15 |
Citation information |
Advanced Materials, 36, 2309518-2309518 (2024) |
Abbreviation of Journal Name |
Adv. Mater. |
DOI |
10.1002/adma.202309518 |
Graphical Abstract |
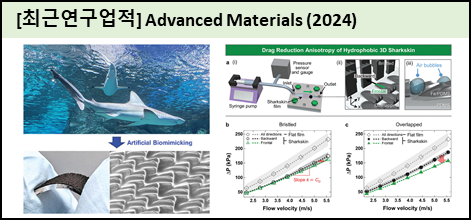 |
Abstract |
Natural sharkskin features staggered-overlapped and multilayered architectures of riblet-textured anisotropic microdenticles, exhibiting drag reduction and providing a flexible yet strong armor. However, the artificial fabrication of three-dimensional (3D) sharkskin with these unique functionalities and mechanical integrity is a challenge using conventional techniques. In this study, it is reported on the facile microfabrication of multilayered 3D sharkskin through the magnetic actuation of polymeric composites and subsequent chemical shape fixation by casting thin polymeric films. The fabricated hydrophobic sharkskin, with geometric symmetry breaking, achieves anisotropic drag reduction in frontal and backward flow directions against the riblet-textured microdenticles. For mechanical integrity, hard-on-soft multilayered mechanical properties are realized by coating the polymeric sharkskin with thin layers of zinc oxide and platinum, which have higher hardness and recovery behaviors than the polymer. This multilayered hard-on-soft sharkskin exhibits friction anisotropy, mechanical robustness, and structural recovery. Furthermore, coating the MXene nanosheets provides the fabricated sharkskin with a low electrical resistance of ≈5.3 Ω, which leads to high Joule heating (≈229.9 °C at 2.75 V). The proposed magnetomechanical actuation-assisted microfabrication strategy is expected to facilitate the development of devices requiring multifunctional microtextures. |
|